Remain Ahead with Proactive Welding Inspection Service Solutions
The Essential Kinds of Welding Solutions Every Industry Must Understand About
In the vast landscape of commercial operations, the value of welding services can not be underrated. Welding is an essential procedure that joins materials together, ensuring architectural integrity and performance across numerous industries. Recognizing the necessary types of welding solutions that satisfy particular sector needs is crucial for optimum efficiency and security. From the conventional yet reputable arc welding to the accuracy of laser beam of light welding, each technique offers distinctive benefits and applications that drive the efficiency and high quality of manufacturing. As sectors develop and require for innovative remedies grows, being well-versed in these welding techniques is not just beneficial however crucial for staying competitive and meeting industry requirements.
Arc Welding
Arc welding is a widely made use of welding procedure that uses an electric arc to sign up with metal components with each other. The process entails developing an electrical arc in between the base steel and a consumable electrode, generally made of a comparable material.
Among the essential advantages of arc welding is its ability to bond a vast array of alloys and metals, making it ideal for varied applications. Additionally, arc welding can be executed utilizing different variants, such as shielded steel arc welding (SMAW), gas metal arc welding (GMAW), and flux-cored arc welding (FCAW), each offering specific advantages depending upon the project demands.
Moreover, arc welding is recognized for its simplicity and cost-effectiveness, making it a recommended option for several producers and manufacturers. By grasping the various methods and equipment connected with arc welding, specialists can create high-quality welds effectively and accurately.
Gas Metal Arc Welding (GMAW)
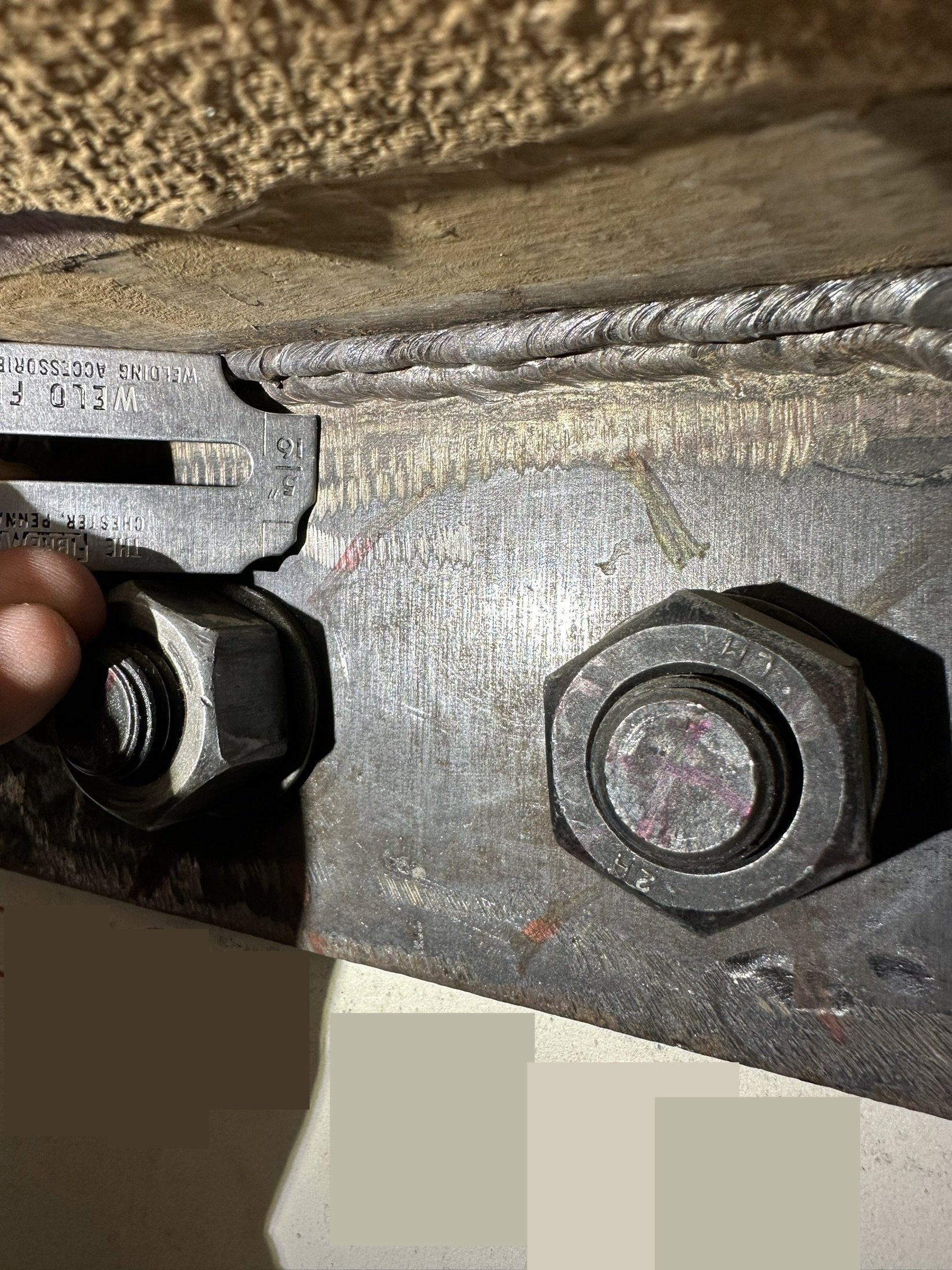
One of the crucial benefits of GMAW is its capacity to produce tidy welds with very little splatter, making it suitable for applications that need a high degree of precision. In addition, GMAW is relatively simple to find out and can be automated for enhanced performance in industrial settings. With correct technique and tools setup, GMAW can create solid, premium welds that fulfill industry requirements. On the whole, GMAW is a versatile welding procedure that supplies efficiency, adaptability, and reliability for a range of welding applications throughout various industries.
Gas Tungsten Arc Welding (GTAW)
Gas Metal Arc Welding (GMAW) supplies phenomenal welding efficiency, and likewise, Gas Tungsten Arc Welding (GTAW) brings a various collection of benefits to the table in the realm of welding services (Welding Inspection Service). GTAW, also referred to as Tungsten Inert Gas (TIG) welding, is a top notch and functional welding procedure frequently made use of in sectors such as aerospace, automotive, and manufacturing

Among the vital benefits of GTAW is its capability to create premium, exact welds on a selection of metals, consisting of light weight aluminum, stainless-steel, and copper alloys. This process enables greater control over the welding arc, resulting in tidy, spatter-free welds with marginal post-weld clean-up needed.
GTAW is also favored for its capacity to bond thin materials without causing warping or distortion, making it ideal for applications where aesthetics and accuracy Visit Your URL are important. Furthermore, the TIG welding process can be made use of with or without filler steel, offering flexibility in welding various joint types and thicknesses.
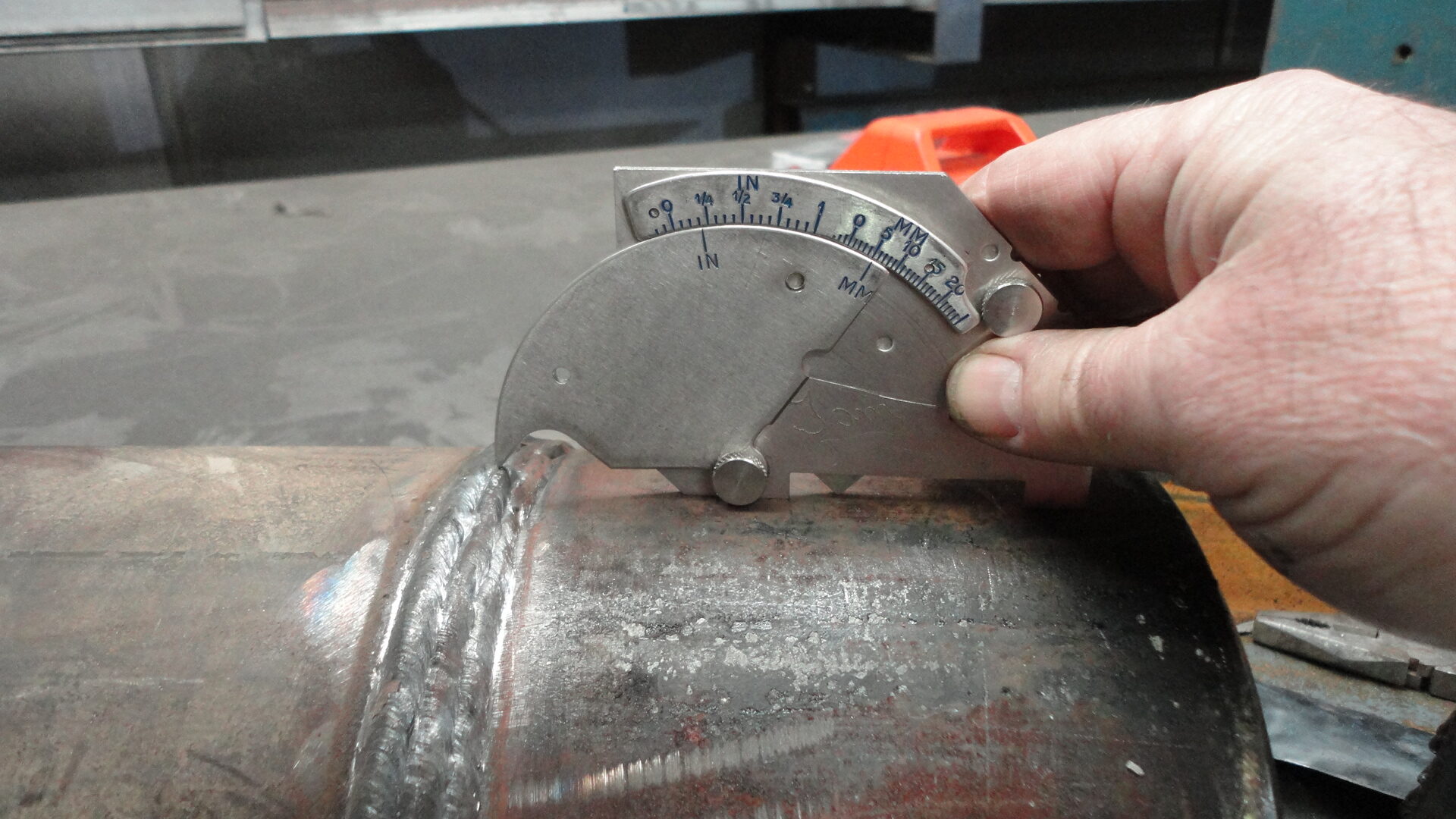
Resistance Welding
A commonly used welding method in various industries due to its performance and performance is Resistance Welding. There are a number of types of resistance welding, consisting of place welding, joint welding, and estimate welding, each fit for particular applications.
Spot welding is typically used in the auto market for joining sheet metal parts. It includes applying 2 copper electrodes to the metal pieces and passing a high present for a short period. Seam welding, on the other hand, is optimal for creating continual joints, such as in the construction of metal containers or pipelines. Forecast welding appropriates for welding nuts, screws, or other bolts onto metal parts.

Laser Light Beam Welding
Making use of an extremely focused laser beam to sign up with and thaw metal parts, laser light beam welding is a exact and reliable welding strategy frequently utilized in numerous markets. This advanced approach uses several benefits, including marginal distortion, high welding speeds, and the ability to weld materials with high accuracy.
Laser light beam welding works by guiding a laser light beam at the workpiece, which creates a liquified pool that merges the products together upon solidification. The procedure is non-contact, suggesting there is no demand for the welding device to touch the workpiece, lowering the risk of contamination or damages. Additionally, the concentrated beam enables for deep weld infiltration and narrow weld joints, making it optimal for applications calling for high accuracy and stamina.
Industries such as automotive, aerospace, electronics, and clinical device manufacturing often rely upon laser light beam welding for its ability to create high-quality welds with very little heat-affected areas. As technology remains to development, laser welding is anticipated to play an increasingly considerable duty in the fabrication of elaborate elements throughout numerous markets.
Final Thought
To conclude, recognizing the important sorts of welding solutions such as Arc Welding, Gas Steel Arc Welding (GMAW), Gas Tungsten Arc Welding (GTAW), Resistance Welding, and Laser Light beam Welding is crucial for each market. Each of these techniques plays an one-of-a-kind duty in the manufacturing and construction processes, guaranteeing sturdy and solid links for different products. By knowing these welding solutions, sectors can make enlightened choices concerning which approach ideal matches their details demands.
From the typical yet reliable arc welding to the precision of laser beam welding, each approach supplies unique benefits and applications that drive the efficiency and high quality of production.Arc welding is an extensively utilized welding procedure that makes use of an electric arc to join metal elements with each other.Gas Steel Arc Welding (GMAW) is a very reliable and frequently utilized welding process in numerous industries for signing read up with metal elements with each other making use of a securing gas and a consumable electrode. There are link numerous kinds of resistance welding, consisting of spot welding, seam welding, and estimate welding, each fit for particular applications.
In conclusion, understanding the essential kinds of welding services such as Arc Welding, Gas Metal Arc Welding (GMAW), Gas Tungsten Arc Welding (GTAW), Resistance Welding, and Laser Beam of light Welding is critical for every market. - Welding Inspection Service